La soldadura MIG usa gases inertes para metales no ferrosos con acabados limpios; la MAG emplea gases activos, óptima en aceros, mayor penetración y productividad industrial.
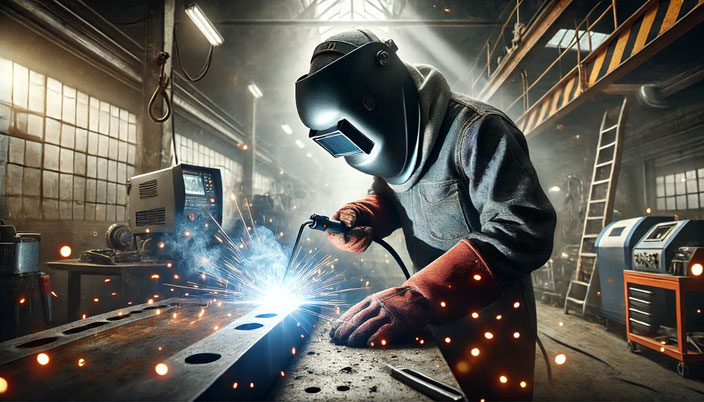
1.- Tipo de gas de protección:
- MIG (Metal Inert Gas): Emplea gases inertes como el argón o mezclas con helio, que no reaccionan químicamente con el baño de fusión.
- MAG (Metal Active Gas): Utiliza un gas activo, generalmente mezclas de argón con CO₂ o con O₂, que sí pueden reaccionar con el baño fundido, alterando ligeramente las propiedades del cordón.
2.- Aplicación en diferentes metales:
- MIG: Adecuada para metales no ferrosos, como aluminio y cobre, donde la protección inerte evita la oxidación y contaminación.
- MAG: Más común en acero al carbono y aceros inoxidables, donde el gas activo mejora la penetración y estabilidad del arco, resultando en un cordón sólido y resistente.
3.- Calidad y aspecto del cordón:
- MIG: Ofrece cordones limpios, con menos oxidación y salpicaduras. Es ideal cuando la apariencia del cordón es importante o cuando se necesita una excelente calidad superficial.
- MAG: Aunque puede generar algo más de salpicaduras, su nivel de productividad y fiabilidad en materiales ferrosos lo hace preferido en entornos industriales pesados.
4.- Control del baño de fusión y el arco:
- MIG: La atmósfera inerte permite un control más predecible del baño, facilitando cordones uniformes, sobre todo en metales delicados.
- MAG: El gas activo influye en la naturaleza del arco, ofreciendo una buena penetración en aceros, aunque requiere un ajuste cuidadoso de parámetros para obtener resultados óptimos.
5.- Aplicaciones típicas:
- MIG: Sectores aeroespacial, automotriz en componentes ligeros, trabajos en aluminio y otros materiales no ferrosos con altas exigencias de acabado.
- MAG: Industria metalmecánica pesada, construcción, fabricación de estructuras de acero, tanques y tuberías, donde se valoran rapidez y robustez.