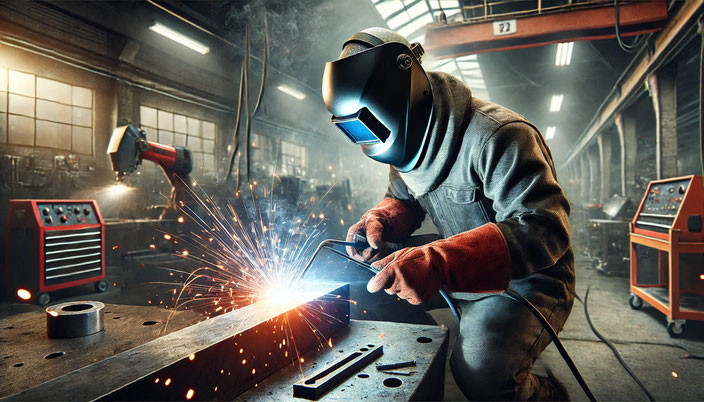
1. Facilidad de uso y aprendizaje:
- La soldadura MIG (Metal Inert Gas) es reconocida por su curva de aprendizaje relativamente corta, lo que permite a operarios nuevos obtener resultados consistentes con menos horas de práctica.
- Al alimentar el alambre automáticamente y mantener un arco constante, las soldadoras MIG facilitan el trabajo del usuario, evitando pausas para cambiar el electrodo y reduciendo el tiempo de soldadura.
- Esta simplicidad hace que la soldadura MIG sea ideal tanto para principiantes como para soldadores experimentados que buscan mayor eficiencia en la producción.
- Además, las configuraciones de parámetros suelen ser más sencillas y predecibles, permitiendo un mejor control sobre la calidad del cordón y la estética de la unión.
2. Versatilidad en materiales y grosores:
- La soldadura MIG puede aplicarse a una amplia gama de metales, incluyendo acero al carbono, acero inoxidable y aluminio, adaptándose así a múltiples sectores industriales.
- Su capacidad para soldar metales de espesores diversos la convierte en una herramienta atractiva tanto para pequeñas reparaciones como para la fabricación de grandes estructuras.
- Gracias a la variedad de gases de protección disponibles (argón, CO₂ o mezclas especiales), es posible ajustar el proceso para mejorar la penetración, la estabilidad del arco y la calidad del cordón, según las necesidades del proyecto.
- Esta versatilidad la hace indispensable en talleres metalmecánicos, carpinterías metálicas, industrias automotrices y fábricas donde se requieren uniones rápidas y fiables.
3. Alta productividad y menor tiempo muerto:
- Al no necesitar reemplazar electrodos constantemente, el proceso MIG permite trabajar de forma continua, maximizando la velocidad de producción.
- El alambre continuo y los sistemas de carrete interno o externo minimizan interrupciones, reduciendo el tiempo de preparación entre cordones.
- Esto se traduce en menor fatiga para el soldador, mayor productividad y, a la larga, una optimización significativa en el uso del tiempo y los recursos.
- En entornos industriales donde la eficiencia es clave, la soldadura MIG suele ser la opción preferida para mantener la competitividad y cumplir con plazos exigentes.
4. Calidad uniforme y estética del cordón:
- La estabilidad del arco y el control del metal de aporte permiten obtener cordones de soldadura limpios, uniformes y de buena apariencia estética.
- Una soldadura MIG bien ajustada presenta menos salpicaduras, reduciendo la necesidad de retrabajos o limpieza posterior.
- Esto no solo ahorra tiempo y esfuerzo, sino que también mejora la presentación del producto final, un factor clave cuando la apariencia importa.
- La consistencia en el resultado ayuda a mantener estándares elevados de calidad, ya sea en la fabricación en serie de componentes o en proyectos especiales de alta exigencia.
5. Facilidad en la automatización e integración en líneas de producción:
- El proceso MIG se presta muy bien para su automatización, convirtiéndolo en una opción frecuente en líneas de producción con robots de soldadura.
- Esta integración facilita la repetitividad y reduce la variabilidad humana, llevando la calidad y la productividad a niveles aún más altos.
- En grandes plantas industriales, la combinación de soldadura MIG con sistemas de automatización y control numérico permite obtener un flujo de trabajo más eficiente, seguro y confiable.
- Al adaptarse fácilmente a herramientas robóticas, la soldadura MIG se convierte en un pilar esencial de las estrategias de manufactura avanzada.